Success Stories: How Businesses in NJ Reduced Workplace Injuries
Introduction to Workplace Safety
Workplace safety is a critical component of business operations, and New Jersey has set a benchmark in implementing effective strategies to reduce workplace injuries. Companies across the state have successfully implemented measures that not only ensure employee well-being but also enhance productivity and morale. This blog post explores some inspiring success stories from businesses in New Jersey that have significantly reduced workplace injuries.
Comprehensive Safety Training Programs
One of the key strategies employed by NJ businesses is the implementation of comprehensive safety training programs. These programs are designed to educate employees on potential hazards and safe practices tailored to their specific roles. Companies have found that regular training sessions, including workshops and simulations, help reinforce safety protocols and create a culture of vigilance.
For instance, a manufacturing firm in Newark conducted monthly safety drills and offered incentives for employees who actively participated in safety initiatives. This approach not only reduced the number of injuries but also empowered employees to take ownership of their safety practices.
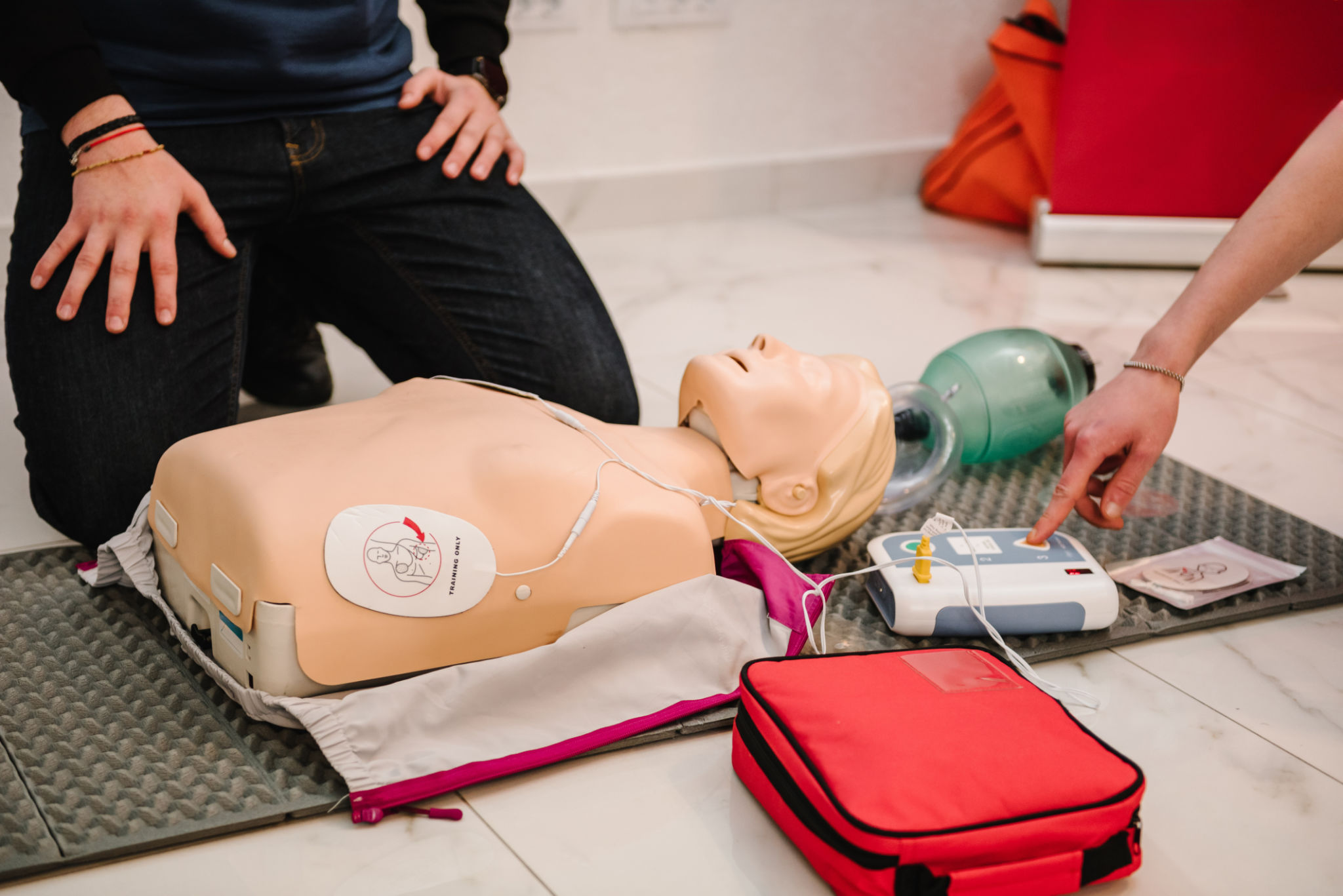
Investment in Advanced Technology
In addition to training, many NJ businesses have invested in advanced technology to monitor and prevent workplace injuries. These technologies include wearable devices that track physical strain, automated machinery with built-in safety features, and comprehensive data analytics systems that predict potential hazards.
A logistics company in Jersey City implemented sensor technology in their warehouses to monitor employee movements and identify unsafe practices. As a result, they saw a significant decrease in incidents related to manual handling and lifting.
Employee Engagement and Feedback
Engaging employees in safety discussions and encouraging their feedback has been another effective strategy. Many businesses have established safety committees comprising employees from various departments to discuss safety concerns and suggest improvements.
A retail chain in NJ formed a safety committee that met bi-weekly to review incident reports and brainstorm preventive measures. This collaborative approach not only improved safety measures but also fostered a sense of community and shared responsibility among staff members.
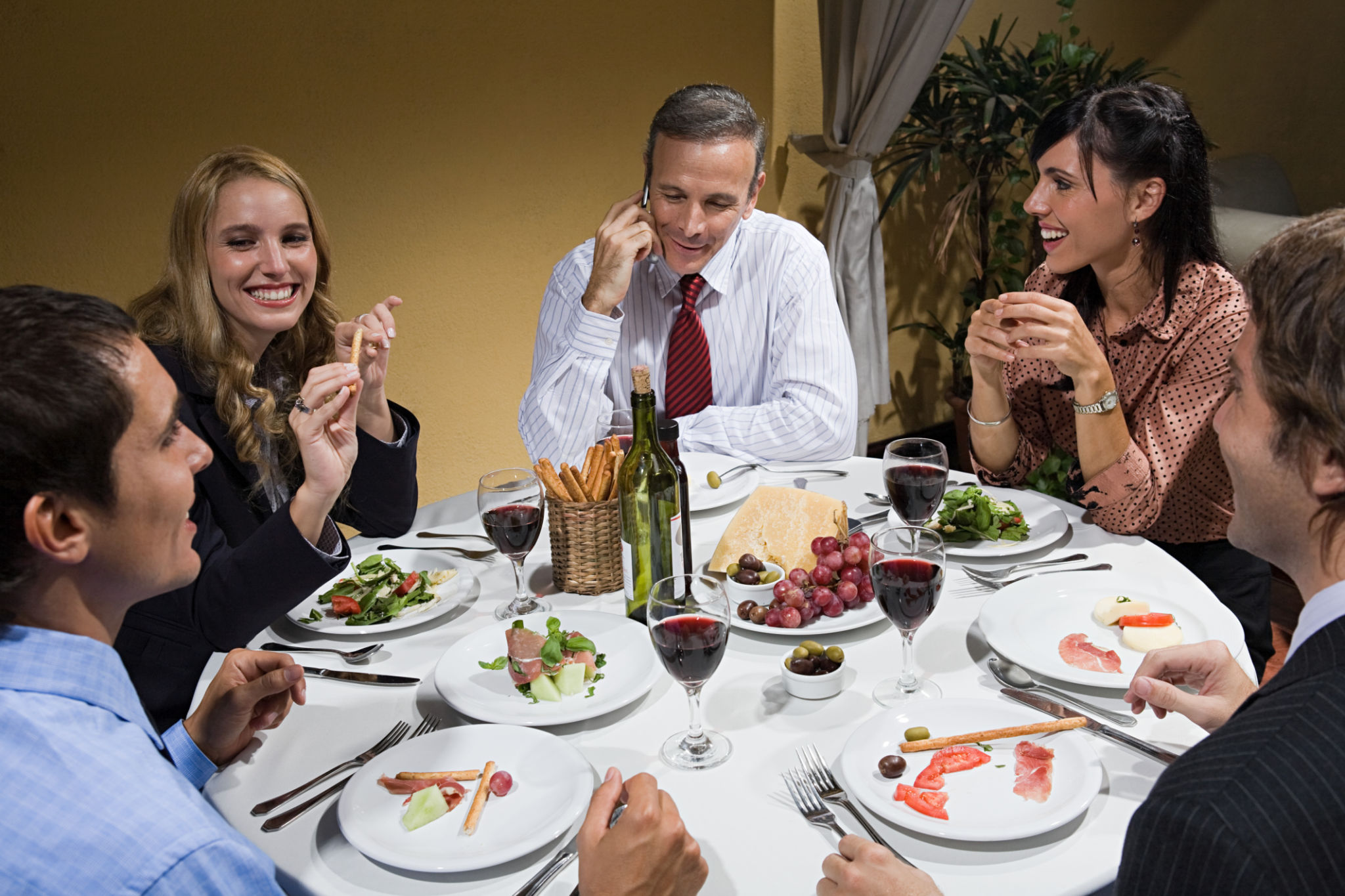
Regular Safety Audits and Inspections
Regular audits and inspections play a crucial role in maintaining workplace safety. By systematically reviewing safety protocols and identifying potential risks, businesses can take proactive measures to address issues before they escalate into serious incidents.
An energy company based in Trenton employed a team of safety inspectors who conducted quarterly audits across all facilities. These audits helped uncover hidden risks and ensured compliance with state and federal regulations, leading to a safer working environment.
The Impact of Reduced Workplace Injuries
The impact of these strategies extends beyond employee safety. Businesses have reported increased productivity, lower insurance premiums, and improved employee satisfaction as a result of their enhanced safety measures. Moreover, a safe work environment boosts the company's reputation, attracting skilled workers who value their well-being.
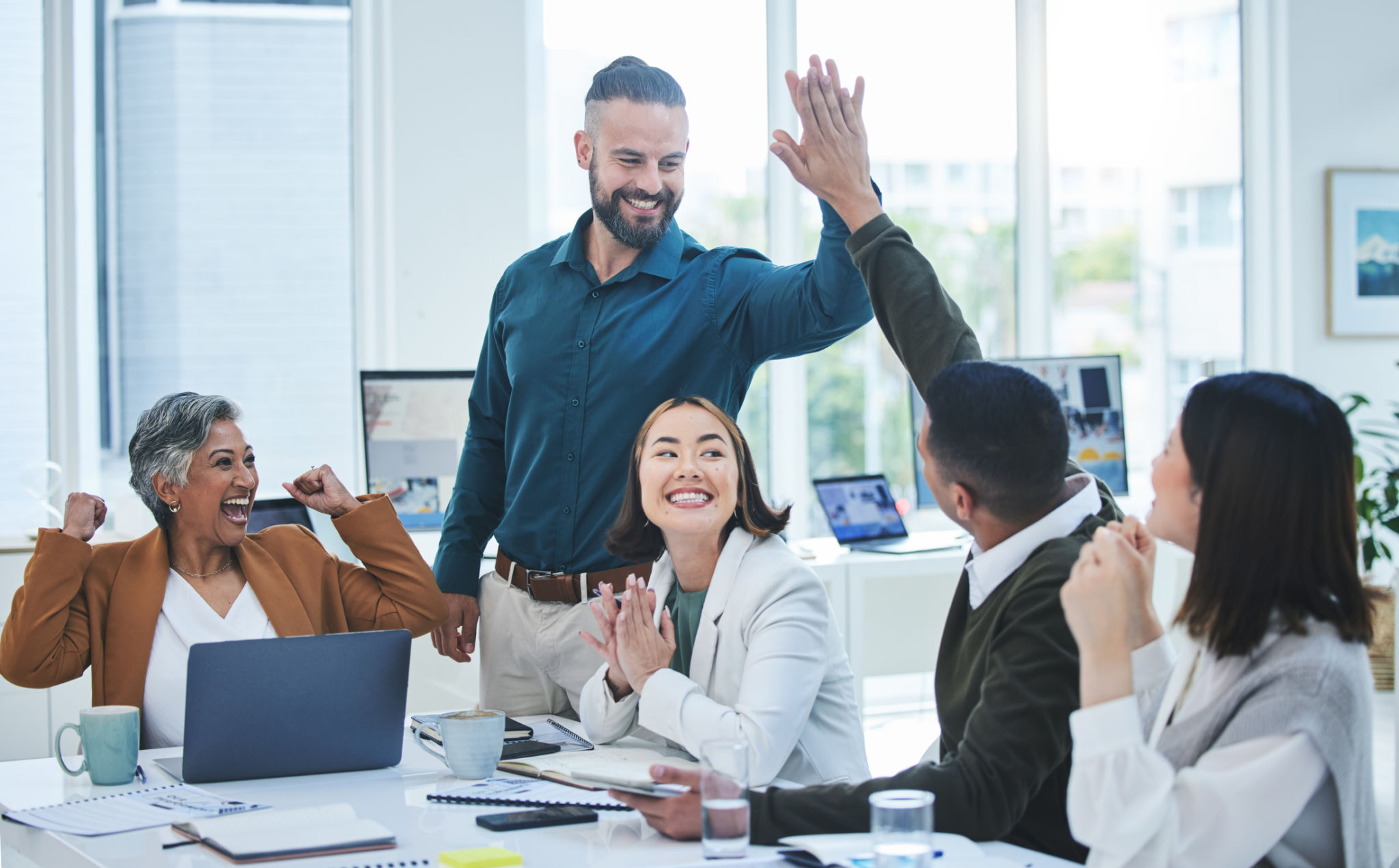
Conclusion
New Jersey businesses have demonstrated that investing in workplace safety is not only beneficial for employees but also advantageous for the overall success of the company. By adopting comprehensive training programs, leveraging technology, engaging employees, and conducting regular audits, these businesses have set an example for others to follow.
As more companies recognize the importance of workplace safety, the collective efforts will undoubtedly lead to safer working environments across industries. New Jersey continues to lead the way in this crucial aspect of business management.